Forming
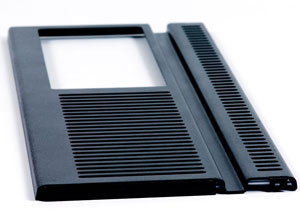
Press Brakes are the most cost effective machinery used for forming low to medium volume quantities of sheet metal. In order to properly form sheet metal, a punch and die are used that best suit the application. The three most common methods of forming are bottom bending, air bending, and coining. All methods have advantages and disadvantages and the inside radius required for the bend usually determines which approach to take. When forming metal, the pressure exerted on the material causes the part to stretch, requiring each bend to have a setback. Below is a chart of K-Factor values that are used to determine the bend deduction required per material type.
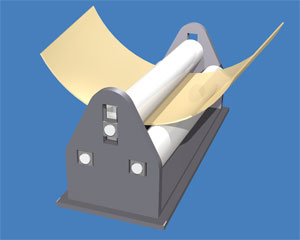
Roll bending is the process of using 3 rollers to form sheet metal and bars into a circular arc. The material is placed in between rollers with two outer rollers on the bottom and one adjustable inner roller that presses on the top. As the material passes through the rollers, the material is force into an arc and eventually into a cylinder. The radius of the arc is determined by the adjustable inner roller. Fabwest is capable of rolling up to 11GA steel and sheets that are 36'' wide.